在现代制造业蓬勃发展的浪潮中,注塑模具以其无可替代的重要性,成为了支撑产业进步的中流砥柱。从日常生活中触手可及的手机外壳、汽车内饰,到高科技领域的复杂电子零部件,注塑模具的应用广泛覆盖汽车、电子、家电、医疗等众多核心产业,是推动这些行业不断创新与发展的关键要素。对于投身于这些行业的专业人员而言,深入理解并熟练掌握注塑模具的基础知识,是在工作中取得卓越成果的必备条件。
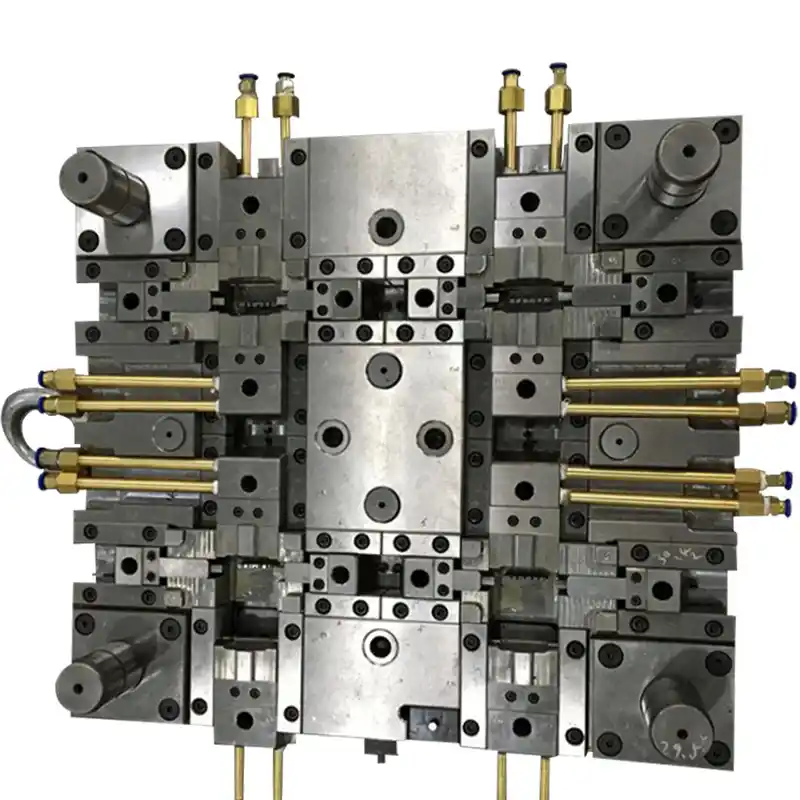
注塑模具作为注塑成型工艺的核心装备,其工作原理融合了材料科学、机械工程和热力学等多学科知识,堪称工业智慧的结晶。注塑过程宛如一场精密的工业交响,每一个步骤都经过精心设计与精确控制。首先,塑料原料在高温和螺杆的共同作用下,迅速熔融并获得良好的流动性。随后,在强大的注射压力推动下,这些熔融态的塑料以精确控制的流速,高速注入精心设计的模具型腔。在这个密闭空间内,塑料如同被赋予生命力一般,均匀地填充型腔的每一处细节,逐渐塑造出与型腔一致的形状。紧接着,通过冷却系统的精确调控,模具内的高温塑料迅速降温固化,最终形成具有特定形状和尺寸精度的塑料制品。
根据模具结构与功能特性的差异,注塑模具主要分为二板模具、三板模具和热流道模具。二板模具结构简单,仅由动模和定模两大部分组成,凭借其高效的开合模动作和较低的制造成本,在对结构复杂度要求不高但追求生产效率的产品制造中广泛应用,如塑料餐具、容器等日常用品的生产。三板模具则在此基础上增加了一个流道板,这一巧妙设计使得点浇口进料得以实现,能够有效避免浇口痕迹对产品外观的影响,因此在对表面质量要求严苛的精密电子产品外壳制造中发挥着关键作用。热流道模具代表了注塑模具的前沿技术,它通过对浇注系统进行持续加热,使流道内的塑料始终保持熔融状态,从而显著减少了废料产生,降低了生产成本,同时提高了生产效率和产品质量的稳定性,在高端塑料制品,如汽车仪表盘、航空航天零部件等的制造中备受青睐。
注塑模具是一个高度精密且复杂的系统,由多个相互协作的关键部分组成。成型零件作为模具的核心,直接与高温熔融的塑料接触,决定了塑料制品的最终形状与尺寸精度。型腔负责塑造产品的外部轮廓,而型芯则用于形成产品的内部结构,二者的精确配合是保证产品质量的基础。浇注系统犹如模具的血液循环系统,负责将熔融塑料快速、均匀地输送到模具型腔的各个角落。主流道作为塑料进入模具的主通道,将注射机喷嘴射出的塑料引入模具;分流道则像树枝般将主流道的塑料分流至各个型腔;浇口则是控制塑料进入型腔速度和流量的关键节点,对塑料制品的成型质量有着重要影响。导向定位系统是确保模具在开合模过程中动模与定模精确对中的关键装置,常见的导柱与导套相互配合,为模具的运动提供精准的导向,保证模具在频繁开合过程中的稳定性和精度。脱模系统则承担着将成型后的塑料制品顺利从模具中推出的重要任务,通过推杆、推管等机械结构的巧妙设计,在不损伤产品的前提下,高效地完成脱模操作,确保生产过程的连续性。
在注塑模具的设计过程中,每一个环节都需要设计师充分考虑各种因素,以确保模具能够满足生产要求并实现高质量的塑料制品生产。首先,根据塑件的形状、尺寸和精度要求,设计师需要运用丰富的经验和先进的计算机辅助设计(CAD)技术,对模具的整体结构和详细尺寸进行精心规划与优化。对于形状复杂的汽车零部件模具设计,通过 CAD 软件进行多次模拟分析,能够提前发现潜在问题并进行针对性改进,确保模具能够准确复制出产品的复杂形状。其次,合理选择模具材料是保证模具使用寿命和产品质量的关键。模具材料必须具备足够的强度、硬度和耐磨性,以承受注塑过程中的高温、高压以及频繁的开合模动作。在生产高强度塑料制品时,通常选用热作模具钢,其良好的热稳定性和耐磨性能够满足长期、高强度的生产需求。此外,塑料的成型性能,如流动性、收缩率等特性,也是模具设计过程中必须重点考虑的因素。不同种类的塑料具有不同的流动性,流动性差的塑料在注塑过程中容易出现填充不满的情况;而收缩率则会影响塑料制品的最终尺寸精度。通过合理调整模具设计和注塑工艺参数,如浇口尺寸、注射压力、保压时间等,可以有效控制塑料的成型过程,避免出现缩痕、变形等缺陷。
综上所述,注塑模具的基础知识涵盖了从模具的定义、分类,到其内部结构组成以及设计要点等多个层面。只有深入理解并熟练掌握这些知识,才能在实际工作中灵活运用,更好地进行模具设计、制造和使用,为生产高质量、高精度的塑料制品提供坚实保障,进而推动整个制造业朝着更高水平迈进。
注塑模具 http://www.mingyanmj.com/product.html 塑胶模具